 |
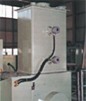 |
 |
A service tank can be attached
to the hopper to maintain the level of powder in the hopper.
This will further improve filling
volume accuracy. |
|
|
 |
 |
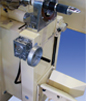 |
 |
With this device, the height
of the bag chair can be adjusted for filling bags of
diverse sizes, simply by turning the handle. |
|
|
 |
|
|
 |
When filling airtight bags, it is necessary
to control backpressure. The ejector unit forces air
out of the bag. |
|
|
|
 |
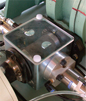 |
 |
When bagging highly fluid powders, powder tends to leak from the nozzle after completion of filling. This device raises volume accuracy and the level of worksite cleanliness.
 |
|
|
 |
|
|
 |
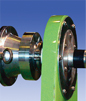 |
 |
A small but highly sensitive
metal detector can be attached to the rear of the nozzle
section. If it detects a metal fragment, the detector
stops the Packer and sounds an alarm. |
|
|
|
 |
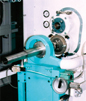 |
 |
When changing the type of
powder to be bagged, the force-feed attachment effectively
forces out any powder remaining in the Packer unit, thereby
improving work efficiency. |
|
|
 |
|
|
 |
 |
 |
This option attaches to the
nozzle section of the AMO Packer to enable filling of
open-mouth bags. Attachment and removal are simple, and
can be completed in a short time. |
|
|
|
 |
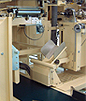 |
 |
The Bag Tipping Guide attaches
to the Packer and the belt conveyor in front of the Packer.
It controls the tipping of the bag thereby reducing powder
spillage. Moreover, this unit is essential for raising
bag sealing precision. |
|
|
 |
|
|
 |
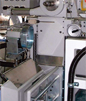 |
 |
On completion of filling,
this unit safely tips the bag onto one side and prevents
the bag from becoming soiled or damaged. If using kraft
paper bags, an air ejector function can also be applied. |
|
|
|
 |
The small amount of powder remaining in
the nozzle after filling is blown into the bag with compressed
air, raising volume accuracy and improving worksite cleanliness. |
|
|
 |
|
|
 |
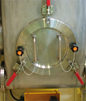 |
 |
A hatch is set into the side
of the Packer hopper to enable internal cleaning and
inspection when changing powder type. |
|
|
|
 |
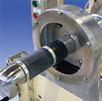 |
 |
After completion of filling,
the expansion nozzle contracts and separates from the
bag. This option captures powder that escapes upon removal
of the bag from the nozzle. |
|
|
 |
|
|
 |
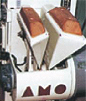 |
 |
The vibrating bag chair raises
fill density when bagging bran and other powders with
low specific gravity. It does not affect quantity accuracy. |
|
|
 |
 |
When bagging powders with adhesive properties
or low fluidity, forcing air into the powder as it moves
through the Packer can improve flow. The ring-nozzle
unit is one such device.
 |
|
|