|
 |
We provide the machinery and facilities for bagging of powders,as fully automated system solutions. |
|
|

Broadly, there are two main bag types - the open bag and the valve bag. Although the
multi-purpose open bag is widely used, the AMO bagging
system is designed basically for the valve bag.
The reason for this is valve bags have considerable advantages in
terms of cleanliness, safety and efficiency.
For open-bag filling, the entire top of the bag is the mouth and powder is dropped
into the bag from above. In contrast, the valve bag is filled through a valve
built into one corner at the top of the bag. A filler nozzle is inserted into
the valve, maintaining a closed environment as the bag is filled.
With a valve bag, the Packer unit will complete the basic processes of filling;
there is no need for secondary processes, such as machine sewing of the bag. Another
considerable merit is that the valve bag enables smaller bag dimensions, with
a higher fill density. |
|
|
 |
Types of valve bags & sealing methods |
 |
Inner Sealed Valve Type |
The valve is inside the valve bag, and the bag is sealed with
an adhesive sealing label. As the valve is inside, the possibility
of powder spillage after filling is reduced considerably. The
sealing machine covers that sealing label with adhesive and seals
the bag. This method eliminates powder spillage after sealing
and prevents foreign materials from entering the bag. The AMO
system uses the inner valve bag for automated sealing. |
 |
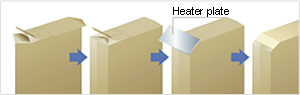 |
 |
Inner Sleeve Valve Type |
This is the general name for bags with internal valves. The Inner
Sealed Valve Type, above, is one variation of the Inner Sleeve
Valve Type. As the bag fills, the powder pushes the valve upward,
effectively closing the valve and thereby preventing powder spillage.
In other words, simply filling the inner sleeve valve bag prevents
spillage of contents. |
 |
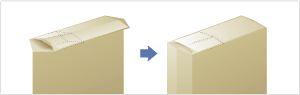 |
 |
External Sleeve Valve Type |
A bag with an external sleeve valve appears to have a tube extending
from the bag. After filling, the bag is closed by folding the external
sleeve valve. Adhesive or other sealants are not necessary, and
the bag is effectively sealed simply by folding the valve. This
valve bag and sealing method are thus often used for manual bagging
operations. The valve can also be heat-sealed for complete closure. |
 |
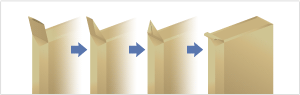 |
 |
Bag Specifications |
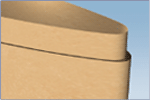
Kraft Paper Bags
Paper is widely used as the bag material in
bagging of powders. It is the standard for many kinds of bags,
due to cost, strength, ease of handling and other features. |
 |
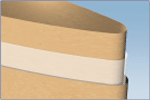
Polyvinyl-Kraft Paper Bags
A layer of plastic is inserted between layers
of kraft paper. This type of bag features high resistance to moisture
and is used for bagging materials that deteriorate in quality on
contact with air. |
 |
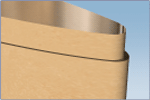
Inner Laminate Paper Bags
These are kraft paper bags laminated with an
innermost layer of plastic or other material. Inner laminate bags
raise the level of hygiene as the powder does not contact paper.
They are highly airtight and resistant to humidity. |
 |
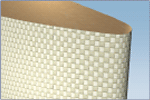
PP-Cross Internal-Layer Bags
From outer to inner, these bags have layers
of PP-Cross, paper and film. They are used particularly for exporting,
and other situations where high bag strength is required. |
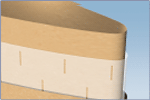
Slit Polyvinyl-Kraft Paper Bags
The plastic film in this bag is slit to allow
air to escape more easily while maintaining a certain level of
humidity resistance. Cement bags are usually this type of inner-valve
bag. |
 |
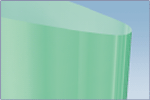
Vinyl Bags
These bags use only plastic. They may be single-
or double-layered and can be many shapes and sizes. |
 |
Layer Composition
Many layering variations of the bag types
and materials outlined here are possible. For example, a
bag might have three layers of kraft paper, and that bag
could then be combined with a vinyl bag. Or, to reduce costs,
a certain layer might be made of recycled paper. |
|
Even with the same materials
and layer compositions, bags can have an infinite variety of valves
and sizes. In the case of valve bags, the diagram below shows how
bags are measured according to length (L), breadth (W) and flat
width (D). Although the volume of the bag is roughly set by the
length and breadth, the flat width is crucial when bagging. This
is because the valve size is in many cases decided by the flat
width. As the AMO Packer inserts a nozzle into the valve, the valve
size must be selected to match the nozzle. |
 |
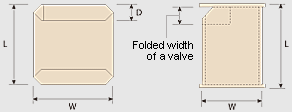 |
|
|
Nakashima Seisakusho Co., Ltd.
Kyoto, JAPAN
TEL.+81-75-691-0004
FAX.+81-75-691-5359 |
Copyright (C) 2006 Nakashima Seisakusho CO,.LTD. All Rights Reserved.
About Personal information | Access map |
|
|
 |
|